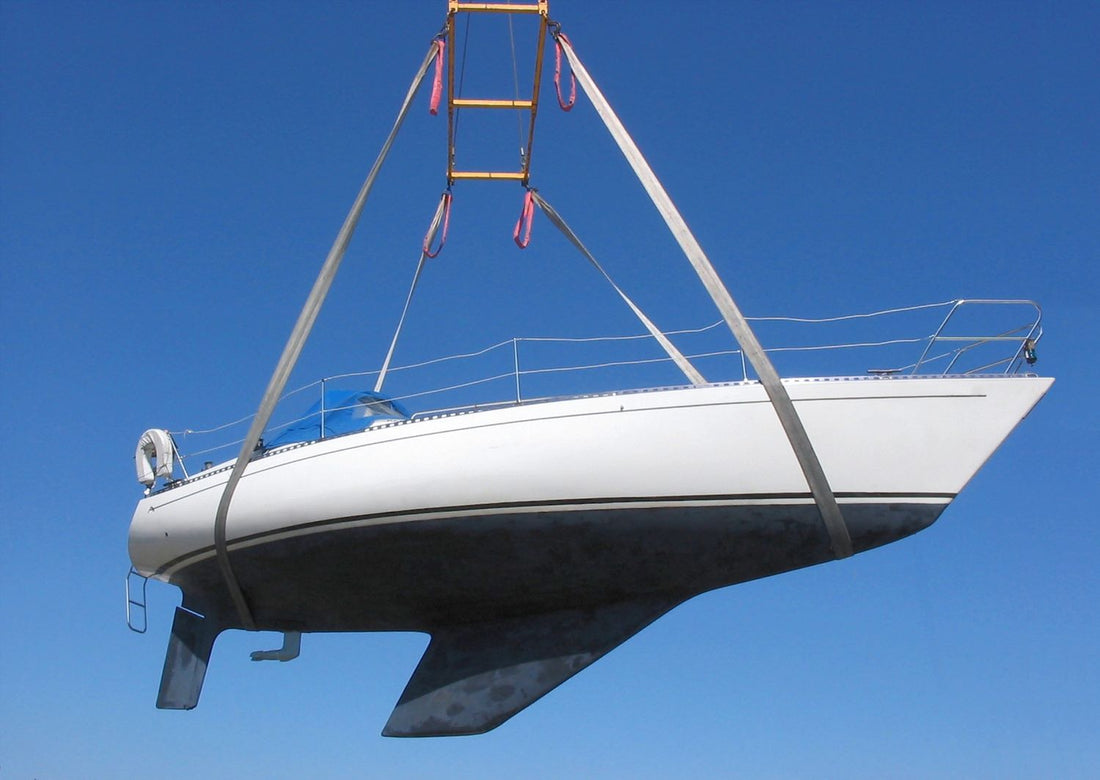
Calculating Bearing Stress for Anchor Shackles & Roundslings
Roundslings offer unique benefits as a synthetic sling. Their higher working load limits, superior performance, and innovative design makes them a primary option for those working in bridge construction, turbine installations, and other lifting and rigging applications.
Oftentimes, these slings connect to cranes and other lifting vehicles via heavy-duty connection hardware - most of the time to anchor shackles. These types of shackles contain a more rounded "O" shape compared to other types, allowing them to take loads from multiple directions and accommodate for wider straps. When it comes to using anchor shackles for lifting tasks, choosing the right size helps to keep the roundsling protected and to minimize the risk of potential sling failure.
A major consideration in choosing the right shackle is the bearing stress of the device. The bearing stress of an anchor shackle plays a critical factor in their safe connections with roundslings. Understanding this metric and how to calculate bearing stress in order to choose the right-sized shackle means the difference in safe and hazardous working conditions.
Read on to learn more about bearing stress and how to calculate it for connection points between anchor shackles and roundslings.
What is Bearing Stress?
Bearing stress occurs when two surfaces come into contact and transmit a force perpendicular to that contact. In essence, when two surfaces intersect, pressure is created, affecting the first object, the second object, or sometimes both.
This types of pressure is commonly found in joints, hitches, or fasteners. The singular connection point undergoes constant push-pull forces, otherwise known as compression and tension as both surfaces pull away from each other. Over time, the constant pressure causes warping of the connection hardware, reducing its capacity to handle the applied load and eventually breaking.
Why is Bearing Stress Important for Roundslings?
Bearing stress plays a crucial role in many lifting and rigging setups, and without correct calculations, the result of poor planning brings about severe consequences.
According to the WSTDA's RS-1 standard on synthetic polyester roundslings, the recommended bearing stress value is 7,000 psi or less. This value came as a result from thorough testing of 400 roundslings across 10 separate manufacturers. When bearing stress values exceed 7,000 psi, the result is damage suffered at the sling connection points. This damage leads to a slew of other events that poses a risk to the load and personnel.
It's vital to keep this bearing stress value threshold in mind when calculating for different anchor shackles. The next part discusses the formula to calculate bearing stress.
How to Calculate Bearing Stress
So, how do you calculate bearing stress for roundslings and their connection hardware?
The simplified version of the formula seems familiar, where bearing stress (σ) equals the applied force (F) divided by the load bearing area (a).
Bearing Stress (σ) |
Applied Force (F) / Load Bearing Area (a) |
However, there are many more components that factor into the equation in order to achieve successful calculations. To be more specific, we need to find out more about the load bearing area of the anchor shackle. We provide a three-step process for calculating bearing stress of an anchor shackle
To use as an example, let's say a roundsling with a WLL of 8,400 lbs. is connected to a Crosby® G-2160 Wide Body Shackle with an inside width of 2", and the sling will be loaded to 6,000 lbs.
1. Calculate Effective Contact Width
The first part of the formula you'll want to calculate is the effective contact width. When roundslings pass through the bow of the anchor shackle, it comes in contact with the body of the shackle itself. Thus, the width the sling uses inside of a shackle is considered an effective contact point, otherwise known as the overall inside width.
The second part of the equation involves the "curved adjustment." The curved adjustment accounts for the percentage of contact that the strap has with the overall inside width of the connection hardware. So, in straight bearing surface applications, the strap typically comes into contact with 100% of the overall inside width of the shackle. This is generally due to the design of the shackle having no curved features that prevent the strap from coming into 100% complete contact with it. However, because anchor shackles feature a rounded "O" shape, there's a curving factor involved with the calculation. WSTDA deemed that for curved bearing surfaces, the effective inside actually comes in contact with 75% of the overall inside width, not 100% like straight bearing surfaces. In reality, the sling will likely sit down in the saddle of the anchor shackle when force is applied.
Both parts - the overall inside width and curved adjustment - are multiplied to come up with the effective contact width, as shown below:
Effective Contact Width
|
Overall Inside Width x Curved Adjustment |
The example from earlier gives us ample information to calculate the effective contact width properly. We know that our 5/8" anchor shackle has an overall inside width of 2". And, because the anchor shackle design contains a rounded "O" ring, we need to adjust for curvature. By plugging in our two values, we get an Effective Contact Width of 1.5".
[Overall Inside Width = 2.0"] x [Curved Adjustment = .75] = [Effective Contact Width = 1.5"]
2. Calculate Load Bearing Area
Once you found the effective contact width of the anchor shackle, the next step in the bearing stress formula is to calculate the load bearing area.
The load bearing area takes the effective contact width of the anchor shackle and makes it three-dimensional using the diameter of the shackle, or connection hardware. This value provides the total area that the strap comes into contact with, as well as the area where force is being applied to (hint: calling back to the original equation).
Load Bearing Area |
Effective Contact Width x Hardware Diameter |
From the example, we know that our effective contact width ended up as 1.5". We also know the diameter of the anchor shackle being 5/8" thick. Therefore, the load bearing area after multiplying these two values ends up being 0.93 in².
[Effective Contact Width = 1.5"] x [Anchor Shackle Diameter = 0.62"] = [Load Bearing Area = 0.93 in²]
3. Calculate Bearing Stress
After finding the load bearing area of the anchor shackle, the last step is to finally come up with the bearing stress value.
We mentioned that in order to find this value, you need to take the applied force of the roundsling and divide it by the load bearing area. To round out the example above, the roundsling pulling the 6,000-lb. load is coming into contact with 0.93 in² of the anchor shackle. Dividing these two values together will come up with the bearing stress metric in pounds per square inch (psi).
[Applied Force = 6,000 lbs.] / [Load Bearing Area = 0.93 in²] = [Bearing Stress = 6,451 psi]
So, the bearing stress of the anchor shackle is 6,451 psi. WSTDA's recommended standard states that bearing stress values for synthetic polyester roundslings stay under 7,000 psi. Since we achieved this through our calculations, the anchor shackle is suitable to use in this application.

Safe Usage of Lifting Slings
Bearing stress calculations seem like a lot, but understanding these components more makes calculating much easier to do. In the end, the biggest understanding is calculating bearing stress means ensuring safe usage of your roundsling at your jobsite.
Calculating bearing stress for roundsling connection points is one of many ways to conduct your due diligence. When it comes to lifting slings, no matter the material, always maintain proper inspection and usage to keep you and others around you safe, including:
- Inspect regularly - look for wear-and-tear, cuts, abrasions, and other damage.
- Follow usage guidelines set by the manufacturer, including working load limits.
- Choose the right type of sling (e.g., material, leg number, etc.) best suited for your application.
- Use sling protection to protect against abrasion and sharp edges.
- Make sure your lifting slings are properly set up with proper hitch configurations and secure attachment points for even load distribution.
- Avoid shock loading.
- Store lifting slings away properly when not in use.
- Remove any damaged lifting slings from service.
More Articles You May Like:
3 Factors to Consider When Choosing Lifting Slings
How Many Legs Do I Need for My Lifting Sling?
Twin-Path Slings from US Cargo Control